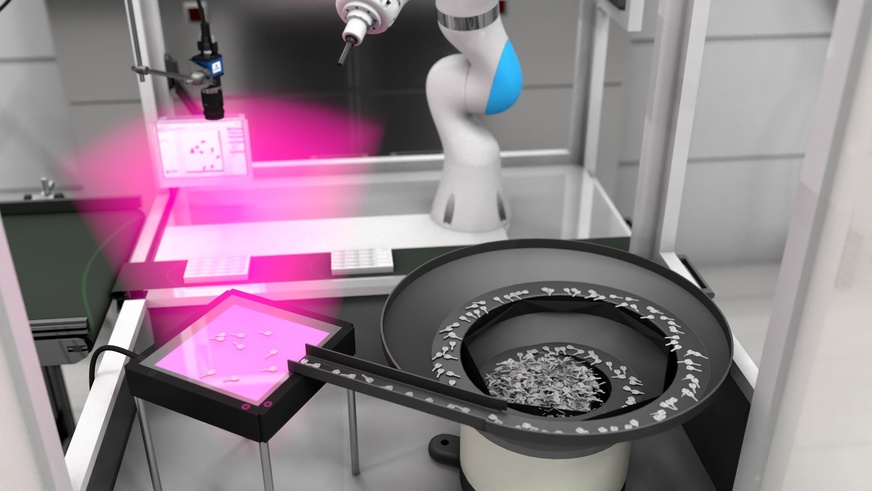
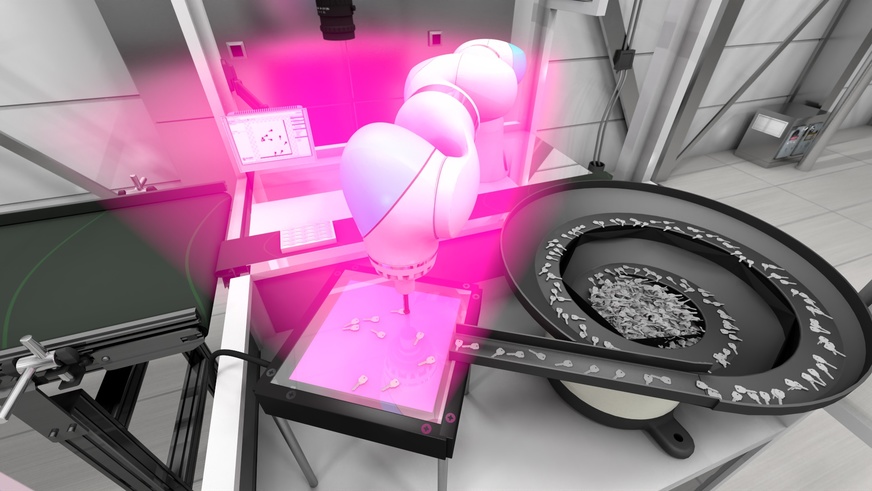
In the course of key manufacturing, pre-made blanks require separation, followed by a robot-assisted pickup ensuring their accurate placement for the next step of the process. Within this precision-driven system, a sequence of actions must be executed with maximum precision to ensure each key emerges flawlessly at the end.
To get them separated, the blanks are transported from the vibratory bowl feeder to a camera-based image system. Equipped with a homogeneous IR backlight, the system effectively highlights the exact position and shape of the keys. The last step involves a robot arm that grabs the identified key blanks, facilitating their subsequent processing.
Challenges
- Speed and throughput: the vision system had to keep up with the fast speed of incoming blanks dictated by the bowl feeder.
- Robust lighting: the uniform illumination was key to the project’s success, ensuring all keys could be located, even under changing ambient lighting conditions.
- Accuracy: the small size of the key blanks required seamless coordination between the camera and the robot arm, as well as precise calibration to account for potential distortions and variations.
Solution
- The HPBACK‘s high brightness is a perfect match for the fast-paced system, ensuring image processing can keep up without compromising on accuracy.
- It provides homogeneous lighting across the entire illuminated area (200x200mm), extending right to the edges. This ensures all keys across the FOV are seen with optimal contrast.
- The chosen backlight in infrared makes it easier to be around the machine and shields workers from intense flashing lights.
- Effective heat management of the lighting setup maintains stable illumination performance.
Alternative uses of backlights
As with any other type of lighting, the angle of illumination can significantly affect the appearance of surface features being inspected. Traditionally, backlights are positioned behind the object, opposite the camera, to create high-contrast silhouettes. By adjusting the angle of the backlight relative to the camera and the inspected object, it is possible to create different effects that highlight specific aspects of the object's surface. For example, placing the backlight on the same side as the camera can help reveal internal structures, voids, or defects that might be otherwise challenging to detect. Backlighting from oblique angles can also highlight curvature and contours on 3D objects. By casting shadows at different angles, the backlight reveals subtle surface variations that may not be apparent using other lighting techniques. This approach underscores the versatility of machine vision technology and the importance of tailoring the lighting setup to the unique requirements of each application.